Basic molding die design standard
The manufacturing process of SunForce is similar to that of foamed beads.
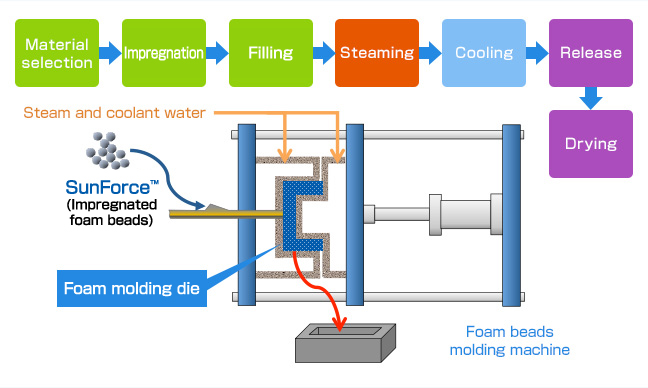
1Material selection
Select a grade of SunForce based on the density of product you wish to achieve. (Refer to Product design guide for selection)
2Impregnation
Before molding, internal cell pressure of SunForce beads of more than 0.3MPa is required. This can be achieved by the following method:
- Fill SunForce beads into a pressuring tank
- Insert pressurizing gas and keep internal tank pressure at 0.4MPa.
- Leave beads in pressurized tank for a certain amount of time. The length of time depends on temperature and pressure set.
- Release pressure and proceed with the molding process.
Pressure opreration for impregnation
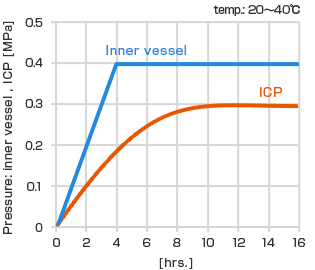
Life time of ICP
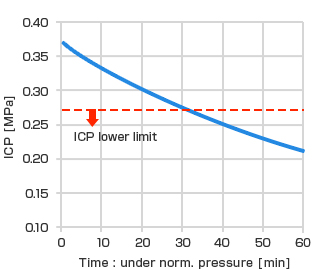
3Molding
1. Filling of SunForce beads
Fill the beads into a closed mold.
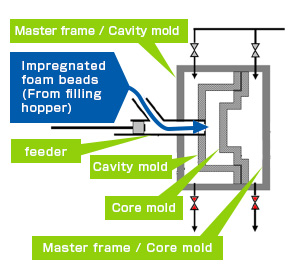
2. Mold heating
Preheat the mold. Insufficient heating of mold will limit the generation of steam required for heating of beads, causing improper expansion and fusion of beads.
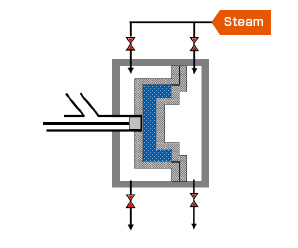
3. One-sided heating
Allow steam to flow in from one side of mold to ensure all air space in between beads is replaced by steam. This ensures proper fusion of beads at all parts of mold.
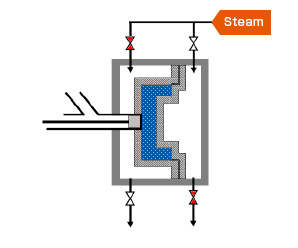
4. Two-sided heating
Continue with heating from both sides of mold until it reaches the molding temperature. Be sure to maintain balance as overheating causes beads to shrink and stick to the mold.
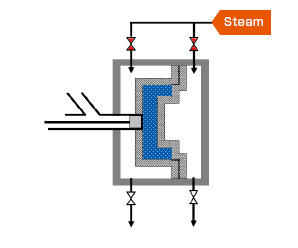
5. Cooling of mold
After heating is complete, proceed with spraying of water to cool the mold.
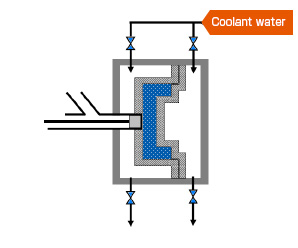
6. Cooling of product
Cool product by vacuuming. By utilizing the latent heat of vaporization, we can quickly reduce the water content in product.
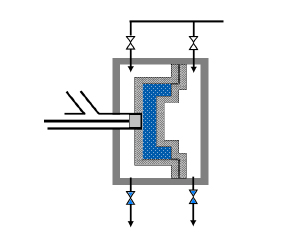
7. Mold release
Eject product from mold by ejector pins or air pressure. Unlike olefin based molded products, products made using SunForce do not undergo shrinkage after molding. The measurements of product are constant after molding.
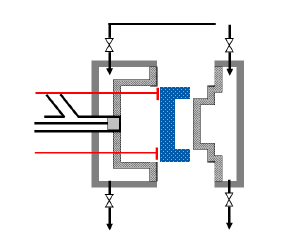
4Drying
About 0.5wt% of moisture content is present in the molded product. The percentage will be lower if vacuum was used during cooling stage (which in this case, drying is not necessary).
To remove most of moisture after molding, keep products in a room under 80℃ for 1 to 6 hours. The drying time depends on thickness of product.
Standard molding conditions
Representative figure, mold products density at 100~200g/L | |
---|---|
(1) Equipment |
|
(2) Impregnation |
|
(3) Molding conditions |
|
Standard molding cycle time
The cycle time depends on grade of SunForce used and the thickness of product. SunForce beads of higher expansion ratio (low density), thinner products = shorter cycle time.
Below is a graph of standard molding time of SunForce
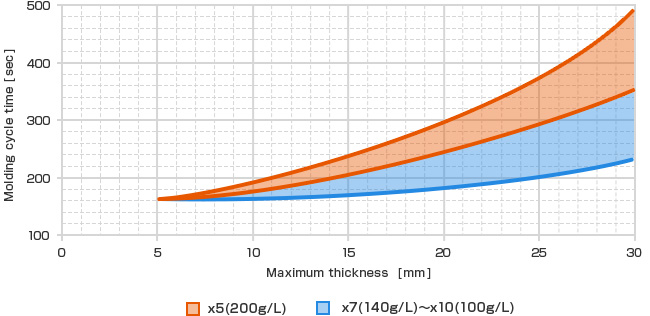