Dimensional accuracy
One of the features of SunForce™ is its dimensional accuracy. Dimensional accuracy indicates the exact dimensions of a material and is an important performance factor for properly functioning the parts that make up industrial products.
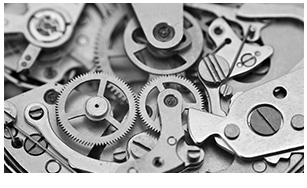
※Image is for illustration purposes
Dimensional accuracy of molded products
The mold shrinkage of SunForce™ is only 0.7%. The low mold shrinkage enables superior dimensional accuracy when compared with other generic polyolefin foam materials, making SunForce™ suitable for parts that require good dimensional accuracy.
Coefficient of linear expansion
The linear expansion coefficient refers to the change in the dimensions of the material with temperature. The greater the value, the greater the dimensional change due to temperature. Although the numerical value for plastic is greater than for metal, SunForce™ assumes the characteristics of PPE plastic with its low coefficient of linear expansion in comparison with other plastics, and the effects of temperature are relatively small. For the measurement values of SunForce™, please refer to the physical properties page (click here).