成形加工ガイド 発泡成形概要、標準成形条件
サンフォースは、一般的な発泡ビーズ成形と同等のプロセスで成形加工していただけます。
加工の流れに従って、各工程をご説明します。
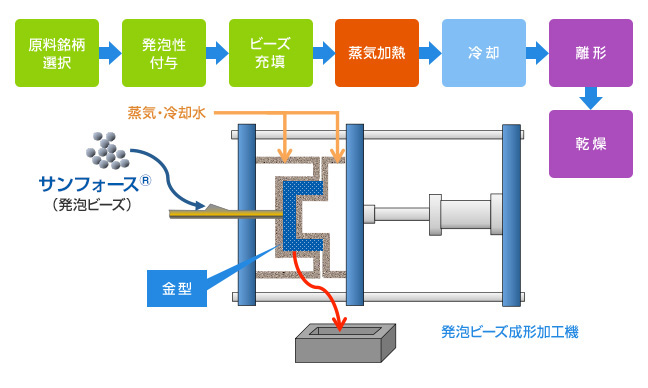
1原料選択
得たい製品倍率に対応する、サンフォースの銘柄を選択頂きます。(製品倍率と原料銘柄については、「製品デザインガイド」をご参照ください)
2発泡性付与
型内で発泡させるために、原料を事前処理する必要があります。成形には原料となる発泡ビーズの気泡内の空気圧を約0.3MPa以上にする必要があります。一般的な発泡ビーズ内気圧を上昇させる方法は下記の通りです。
- 原料ビーズを加圧タンクに投入する。
- 加圧タンク内に圧縮空気を入れて0.4MPaまで昇圧し保持する。
- 一定時間、タンク内圧を0.4MPa保持する。
(必要な加圧保持時間は、温度・圧力によって変化します) - 圧力解放後速やかに成形する。
発泡性付与条件
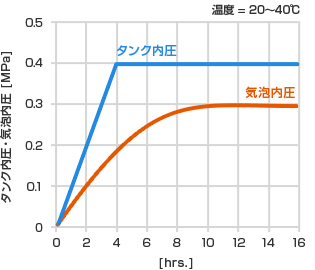
発泡内圧(ICP)の寿命
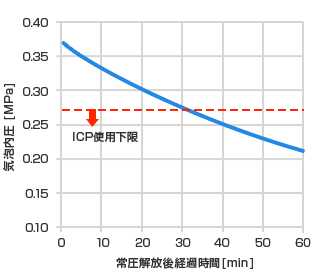
3発泡成形
1. 原料充填
閉じられた金型内に、ビーズを圧縮空気と共に吹き入れ充填します。
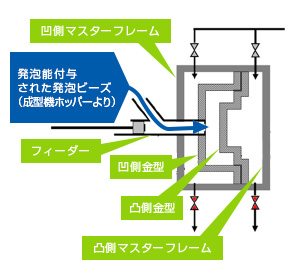
2. 金型加熱
ビーズを素早く加熱するために、金型を予熱します。
不十分だと、空気が完全に蒸気に置換できず、目標蒸気圧力でも、低温となったり、次項以降の昇圧工程の立上りが遅くなり、融着不良や膨張不良の原因となります。
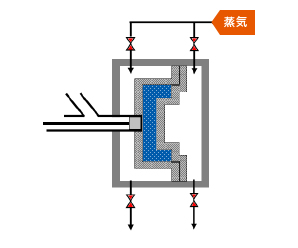
3. 一方加熱
蒸気が金型を通過するように、金型の蒸気を一方から蒸気を吹き入れ、金型内・ビーズ間の空気を蒸気と置換します。不足すると、部分的な融着不良が発生しやすくなります。
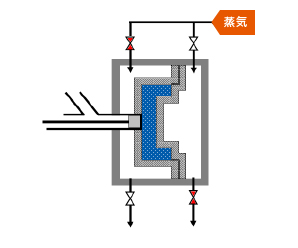
4. 両面加熱
成形温度まで昇温するために、排気バルブを閉じて金型の両面から蒸気を吹き入れます。不足すると、全体的な融着やビーズ膨張不足となり、過剰すぎると収縮や金型への融着などが発生します。
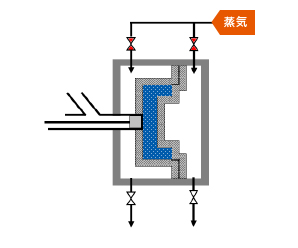
5. 水冷
加熱を終えた製品を冷却するためにまず冷却水を金型裏面より吹き付け熱容量の大きい金型を冷却します。
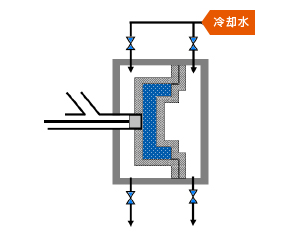
6. 放冷
冷えた金型より伝熱で金型内製品の冷却を行います。
真空引きをして、蒸発潜熱を利用して冷却すると、より早くまた製品内の含水率低減化に効果があります。
発泡成形では、発泡体自体が断熱材となるため、この工程が最も時間を要する場合が多いです。
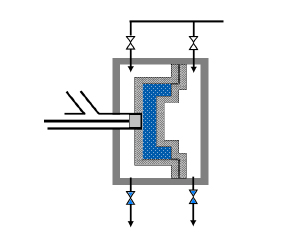
7. 離形
金型を開き、離形ピンまたは圧縮空気で金型から製品を取り出します。
離形直後の製品寸法は、ほぼ最終製品寸法となります。
一般的なオレフィン系の発泡体と異なり成形後の収縮回復がほぼありません。
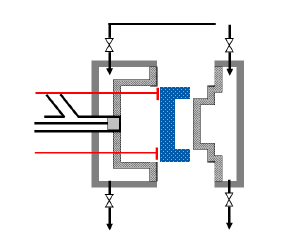
4乾燥
成形直後は製品の表面及び内部に凝縮水が付着しています。内部の含水率は、概ね0.5wt%前後となります。
発泡成形工程の冷却工程で、真空引き冷却を実施した場合は、更に低い含水率となり、特別な乾燥が不要となる場合があります。
発泡成形後、製品内部の含水分除去を行うために、80℃以下の部屋で1~6時間程度乾燥します。乾燥時間は、製品の厚みによって変化します。
標準成形条件
成形品密度=100~200g/Lの場合の代表値 | |
---|---|
(1) 成形設備 |
|
(2) 発泡性付与条件 |
|
(3) 成形条件 |
|
標準成形サイクル
成形サイクルは、発泡倍率と最大肉厚に影響されます。発泡倍率が高い(密度が低い)ほど、肉厚が薄いほど短くなります。
また、製品形状や成形機によっても30%前後は変化します。下記は、サンフォースの標準的な成形サイクルです。
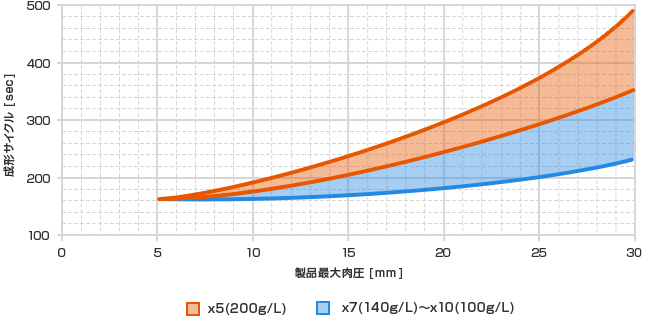