Example 2: Motor vehicles · Batteries
(Heat insulation, Weight saving)
Combining excellent flame retardancy, thermal resistance and high strength, foamed structural material SunForce will contribute to weight reductions and performance enhancements of various automotive parts.
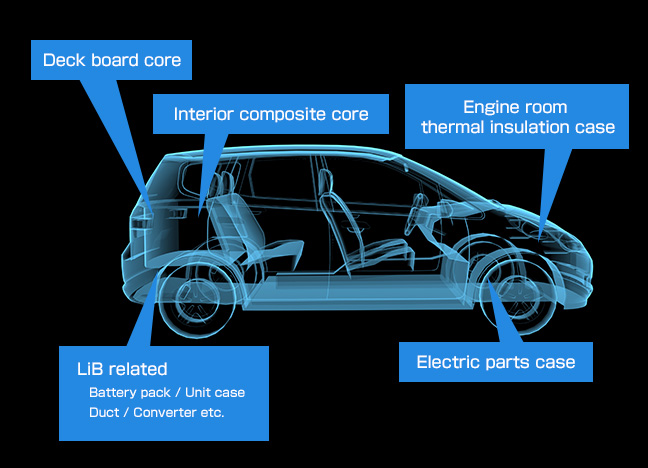
Requirements of automotive industry
Flame retardancy
The current common standard for flame retardant materials used in the internal compartments of motor vehicles is FMVSS 302 (Federal Motor Vehicle Safety Standard).
FMVSS 302 tests horizontal burning speed of materials.
However, the requirements for flame retardancy in some parts of hybrid cars and electric cars are stricter. Materials used in these parts are required to be in compliance with UL-94 V-1/V-0 (more stringent ratings than FMVSS 302).
SunForce, which is developed based on FMVSS 302 standards, is also UL-94 V-0 certified.
Heat resistance and rigidity
Motor vehicles are designed to withstand harsh environments.
The materials used in the engine compartment have to be able to endure high temperature up to 120 degree Celsius.
Even with insulation from the air in the compartment, materials still have to withstand heat of about 80 to 100 degree Celsius.
SunForce can be used in the engine compartment as it is able to withstand 100 degree Celsius without compromising its functionality.
Heat insulation
Lithium ion battery and electronic components such as microcomputers and controllers in modern vehicles require a constant temperature for optimized performance.
Water condensation from cooling of these components can cause problem to the electronics.
To maintain optimal temperature of car interiors, measures such as installation of thermal insulation materials and utilization of A/C air are applied.
SunForce can maintain a proper temperature for these components by insulating heat inside and from the outside.
For usage around lithium ion batteries
As heat is generated during the charging of battery, cooling of the cells becomes necessary before the temperature exceeds the heat resistant temperature of the cells.
On the other hand, heating is required to ensure power generation from the battery is maximized at places with low temperature.
This requires very sophisticated uniform temperature management for battery system which has many cells.
In recent years, the capacity (number of cells) of lithium ion batteries used in vehicles has increased and these batteries cannot depend on natural heat dissipation that is possible in small battery units.
By using SunForce inside the battery case, we can
- Control of air flow from the conditioning system
- Insulate heat from the outside
- Hold cells, cables and fans in place.
A low cost weight-saving example is a battery case which covers and holds battery cells and cables is constructed with SunForce. Ultilizing the design versatility of SunForce, an air-duct to enable cool A/C air into the case is built into the structure.
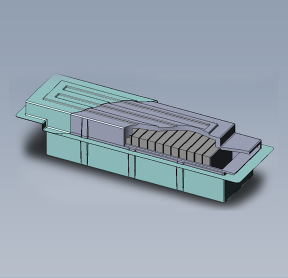
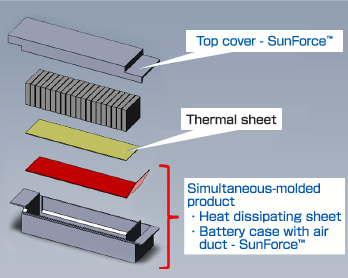
Cooling at high temperature
By utilizing SunForce design like that shown below, cool air from the conditioning system can be guided into the battery and cells can be cooled evenly.
Heat transfer can even be facilitated by using SunForce composite (with metal mesh) at the bottom of the cells.
As the case is thermally insulated from open air, less cooling energy is needed and condensation is prevented.
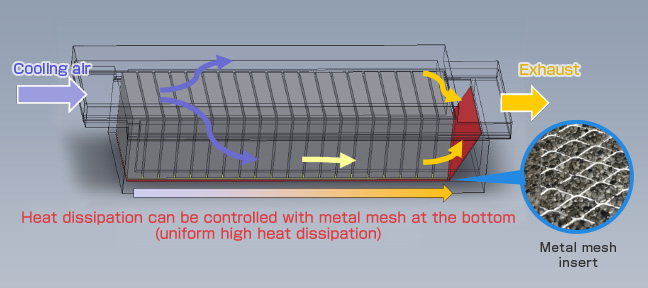
Heating at low temperature
It is well-known that battery system cannot work effectively under excessively low temperature.
To avoid this issue, some EVs or high performance HVs have special built-in heaters to manage the temperatures of their battery cells.
As SunForce keeps the heat inside of the battery unit of electric and hybrid cars, we can prevent heat loss from the battery after the car has stopped. Starting up becomes easier as the battery now requires lesser heating and time to generate high output of power.
Comparing the time of reduction in battery temperature using SunForce
We studied the heat loss effect in lithium ion battery when SunForce is used on the inner side of the aluminum case of the battery.
・ Outside air temp.: -20℃, Start air temp. inside unit: 60℃
・ SunForce specification: [Expansion ratio] 7 times, [Thickness] 10mm and 5mm
・ Outer panels: Aluminum 2mm
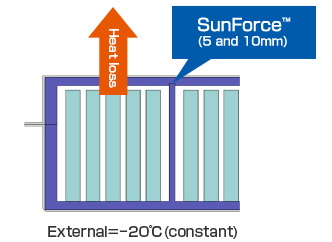
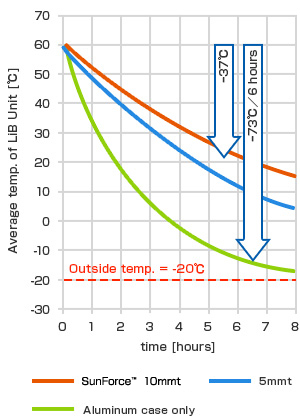
For usage as interior core materials
Many automotive interior applications require heat resistance of more than 80℃ and high-temperature material structure rigidity.
SunForce can also be used in areas like pillars (where airbags, electronic components are installed), deck board etc.
Compared to conventional EPP (expanded polypropylene) foam, SunForce is able to withstand higher temperature, has higher precision in shape and is flame retardant.
As a core material for pillars, SunForce can be shaped and structured to hold airbags and electronics components, leading to parts and weight reductions.
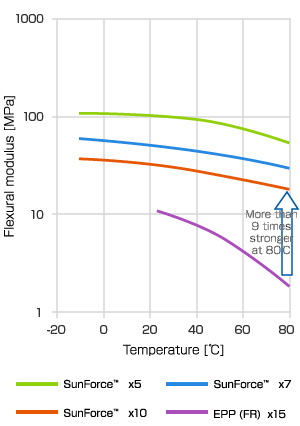
As core material for deck board
Deck boards require light-weight and high flexural modulus simultaneously.
Deck boards are usually made of metal reinforced injection blow molded plastic or a combination of expanded foam material with sheets with high strength.
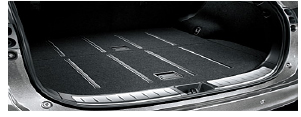
It is difficult for metal reinforcement to reduce weight. However, conventional foamed plastic cannot fulfill the requirements for heat-resistance and flame retardancy.
Unlike these materials, SunForce is able to
- Reduce weight by more than 20%
- Expand free space (using a sleek design)
- Withhold rigidity at high temperature
- Provide safety (as it is flame retardant)
(Same bending strength)
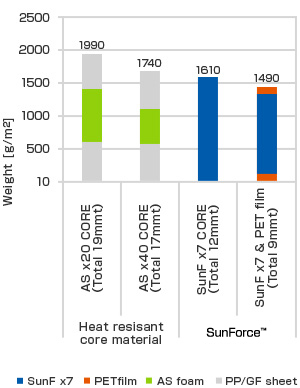